Iron & Steel Technology
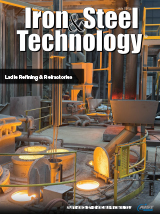
July Issue Now Online!
Ladle Refining & Refractories
Special Features Include:Table of Contents
56
Study of the Vacuum Degassing Process Using the Effective Equilibrium Reaction Zone Model
Advanced steel products made by electric arc furnace steelmaking require vacuum degassing (VD) to meet nitro-gen/hydrogen specifications. An effective equilibrium reaction zone-based VD model was developed to under-stand/optimize the operational parameters and their impact on denitrogenation (deN) rate. The effects of argon injection, vacuum pressure and steel temperature were explored. The calculated deN rates were validated with in-dustrial-scale tank degasser trials. A novel approach was adopted to incorporate bubble-steel interface deN reac-tions in order to replicate plume and eye formation through Ar injection in VD.
72
Challenges for BOF Impact Pad: Redesign Flexible Binder for Improving Performance
The decarbonization and transformation of integrated basic oxygen furnace steelmaking is currently an important challenge. As a charge material with zero CO2 emissions, steel scrap is essential to the decarbonization process. As the amount of steel scrap charged to converters increases, it promotes higher wear of refractories installed on scrap impact zones. A new generation of carbo-resins with low-emission binder system was first introduced for improving flexibility in cold processing, similar to pitch-bonded bricks processed at hot conditions. This work presents a complete comparative evaluation of the novel redesigned flexible binder MgO-C brick against the original resin-pitched one. Customers’ performance is highlighted.
80
Maximization of Steel Ladle Free Open Rate by Using Shop-Specific Production Parameters
This article will demonstrate how Nucor Steel–Berkeley’s shop operating parameters and specific process routes were used to increase ladle free open rate, resulting in less ladle burn opens and improved quality.
84
Multiple-Use Basic Slidegate Plate for Corrosive Steel Casting
Conventionally, corrosion-resistant, basic materials have been applied in slidegate plates for corrosive steel. However, their durability is limited by cracks and sticking/peeling between plates. This article investigates the ef-fects of adding spinel and changing grain size distribution, different carbon raw materials, and changing the amount/size of metal additives. Adding grain size-optimized spinel improved thermal spalling resistance by sup-pressing crack formation with minimal deterioration of corrosion resistance. Furthermore, subsequently adding different carbon and metal additives mitigated sticking/peeling damage and improved oxidation/wear resistance, respectively. Considering all these countermeasures together, multiple-use slidegate plates for corrosive steel grades can be developed.